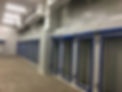
about us
Welcome to Celtic, your premier solution for all your cooling needs. At Celtic, we specialize in designing, supplying, and installing state-of-the-art cooling systems for a variety of industries. Our expertise spans across commercial, industrial, and agricultural sectors, ensuring that we can provide tailored solutions to meet the unique requirements of each client.
​​
Our Team
Our team is composed of highly skilled professionals with extensive experience in the cooling industry. From engineers and technicians to project managers and customer service representatives, every member of our team is dedicated to delivering top-notch service and support. We continuously invest in training and development to ensure our team stays at the forefront of industry advancements and best practices.
​
Our Commitment
What sets Celtic Cooling apart from our competitors is our unwavering commitment to quality and customer satisfaction. We use only the highest quality materials and the latest technologies to ensure our cooling systems are durable, efficient, and environmentally friendly. Our customer-centric approach means we are always focused on meeting and exceeding your expectations.
​
Why Choose Us?
- Expertise: With years of experience in the industry, we have the knowledge and skills to handle projects of any size and complexity.
- Innovation: We stay ahead of industry trends and incorporate the latest technologies into our solutions.
- Quality: We never compromise on quality, ensuring that every product and service we deliver meets the highest standards.
- Customer Satisfaction: Your satisfaction is our top priority. We work closely with you to understand your needs and deliver solutions that exceed your expectations.
​
At Celtic Cooling, we are more than just a cooling company. We are your partners in creating efficient, reliable, and sustainable cooling solutions. Thank you for considering us for your cooling needs. We look forward to working with you.


